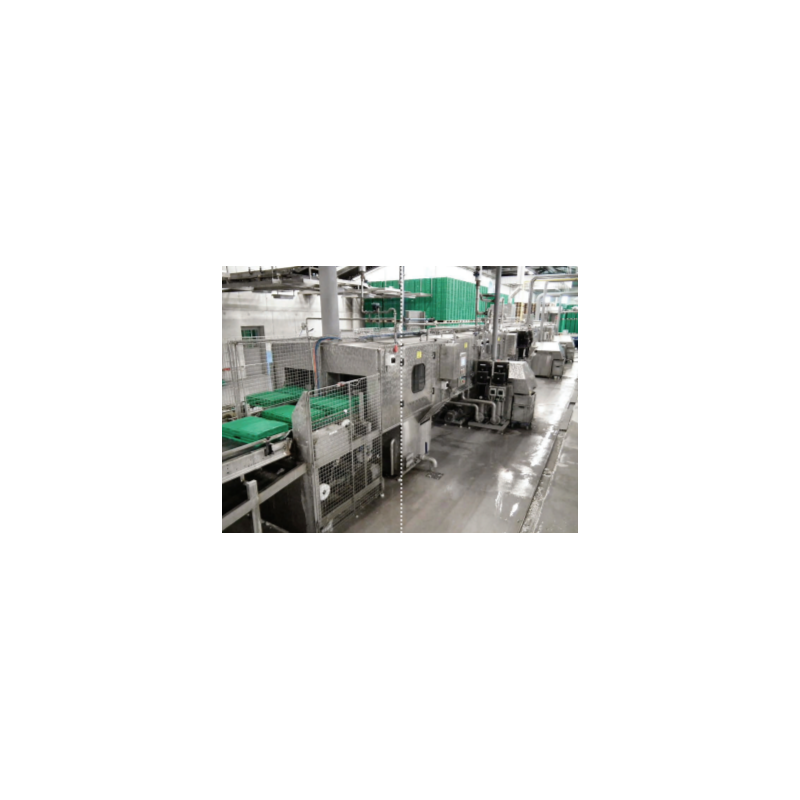
- New
Brüel Systems tunnel washer
For all sectors including meat, bakery, fruit and vegetable, fish, brewery & distribution.
Description
General
■ All sectors including meat, bakery, fruit and vegetable, fish, brewery & distribution
■ All box types including rigid, foldable, bale-arm & nestable
■ Each washer is engineered to meet the specific requirements of the ap plication based on modular con struction.
■ Single or dual lane options accord ing to capacity required. Up to 2400 boxes per hour per lane.
■ Can be integrated into a fully automated washing and handling system including automated in-feed and out feed.
■ Type 304 stainless steel
Infeed
Driven friction rubber belt conveyor. Adjustable supports provide height flexibility to ensure good ergonomic working conditions for operatives.
Pre-rinse zone
For boxes with heavy soiling a prerinse section can be provided. This enables water as well as detergent to be saved by maintaining the quality of the water in the main wash tank for longer.
Dissolving zone
A large number of carefully positioned nozzles ensures that the dirt on the box is efficiently softened prior to the box entering the main wash zone. The length is dictated by the box size and required capacity.
Screw filter
Rotary screw filter ensures that the water is continuously cleaned. An external container collects the separated dirt from the wash water.
Label removal
The system works with pressures up to 38 bar, and the specially designed and positioned nozzles form a strong wash jet directed at the normal label positions. All water is recycled, via a screw filter minimising water consumption.
Washing zone
In the washing zone, the nozzles are located in a spray portal. The washing pressure is typically 6 bar with a spray volume of between 50-120 m3/hr. The wash water is re-circulated via a screw filter.
After-rinse zone
Re-circulated after-rinse with water fed from a separate tank at a pressure of 2 bar and a final fresh water rinse fed direct from the mains. A water-saving device ensures minimum freshwater consumption for the final rinse. A static filter is fitted in the after-rinse tank.
Transport system
For box transport through the tunnel washer, a conveyor (plastic or steel according to the application) is used with carriers and adjustable top and side guiding according to the size and design of the box.
Drying zone
High pressure air knives ensure the required level of dryness of the box. The air is re-circulated and heats up during operation improving the dryer efficiency. The water blown off is returned to the after-rinse zone.
Outfeed
Non-driven roller conveyor.
118 other products in the same category:
- New
Perfectly clean vegetable crates thanks to unique Pivo system
- New
- New
- New
- New
- New
- New
- New
LQ-RCGF Washing-filling-capping 3 In 1 Machine For Juice
- New
- New
- New
Industrial washing-machine & forced air drying module
- New
- New
- New
- New
- New
- New
- New
- New
INDUSTRIAL PASS THROUGH WASHER FOR CRATES, UP TO 100 PCS/H
- New
- New
- New
- New
- New
INDUSTRIAL WASHER FOR 200 L BUGGY WITH STANDARD FILTER
- New
- New
- New
- New
- New