- New
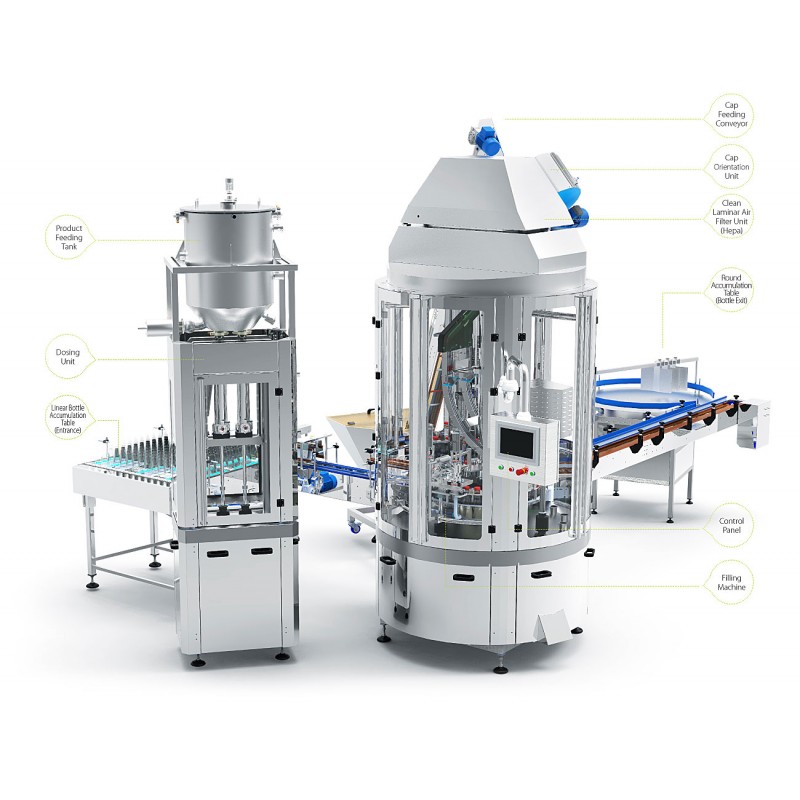
- New
Hygiene Rotary Filler and Capper
The highly flexible and hygienic Inline Cup Filler, from the series AFIC, is solidly built and easy to operate
Description
The Principle Function:
The highly flexible and hygienic Inline Cup Filler, from the series AFIC, is solidly built and easy to operate.
This series is designed for a very high hygienic standard and provides filled and sealed products with a long shelf-life.
The AFR series is available with a packaging output speed of between 3000 and 12,000 containers per hour, depending upon the product, volume, cup size, cup shape, and the head space inside of the filled container.
The stations are designed with high flexibility and all functions are fully servo driven, pneumatic driven, frequency-controlled motor driven, and controlled from the control panel.
The rotary filler and capper can be used for:
- Juices
- Milk
- Yogurt
- Ice cream
- Mayonnaise
- Ketchup
- Honey
- Jam
- Soft cheese
- Hummus
- Tahina
- Salad dressing and many similar products
Machine Frame
The highly hygienic machine frame is one of the most important parts of the filler. The machine table is built with a beveled surface for preventing standing wash water. If wash water is standing on the table and is not drained quickly and completely, microorganisms can grow in the water. These microorganisms can contaminate the product.
The table is fully welded to prevent penetration of cleaning water into the machine base (machine foot).
Door Covers
The door covers are made from tempered glass, adhered into a stainless steel frame. Glass cover doors can never be electrostatically charged like the polycarbonate doors. An electrostatic current allows unsterile dirt to cling to the door when opening.
When closing the doors, this unsterile dust will be shaken off the door and fall into the clean filling machine, contaminating the complete filling area.
Highly Flexible Machine Stations:
Dosing Unit
The highly hygienic, servo driven dosing unit fills highly sensitive and viscose products and can be equipped with a pressure tank up to 2 bar.
Capping Unit
The capping unit is built and designed to align, sterilise (optional), and screw the caps on to the bottles. The location of the caps is made with a round orientation unit or with an orientation conveyor. Sterilising the caps can be integrated into the cap slide, with ozone gas.
The cap screwing unit is made with a magnetic, torque-limited, gear motor, or with a servo-driven spindle. All the parameters are adjustable from the controller of the filling machine.
Linear Bottle Accumulation Table
The Linear Bottle Accumulation Table can feed bottles to, or receive bottles from, the filler.
Cap / Lid Elevator
The Cap / Lid Elevator transports the lids into the cap orientation unit and is available with two transportation conveyors for two different cap colors.
Conveyors
Conveyors connect the different machines / components.
Filling Unit
The high clean filling nozzles for highly sensitive, highly hygienic products. Equipped with the “Seal Back Space Cleaning System”.
Clean Air Station
Clean air is necessary to fill products without preservatives. The filter housing of the unit is built from stainless steel and protects the filter from wash water.
64 other products in the same category:
- New
TPM 1000 fully automatic thermoforming packaging machine
- New
- New
- New
- New
- New
- New
- New
- New
- New