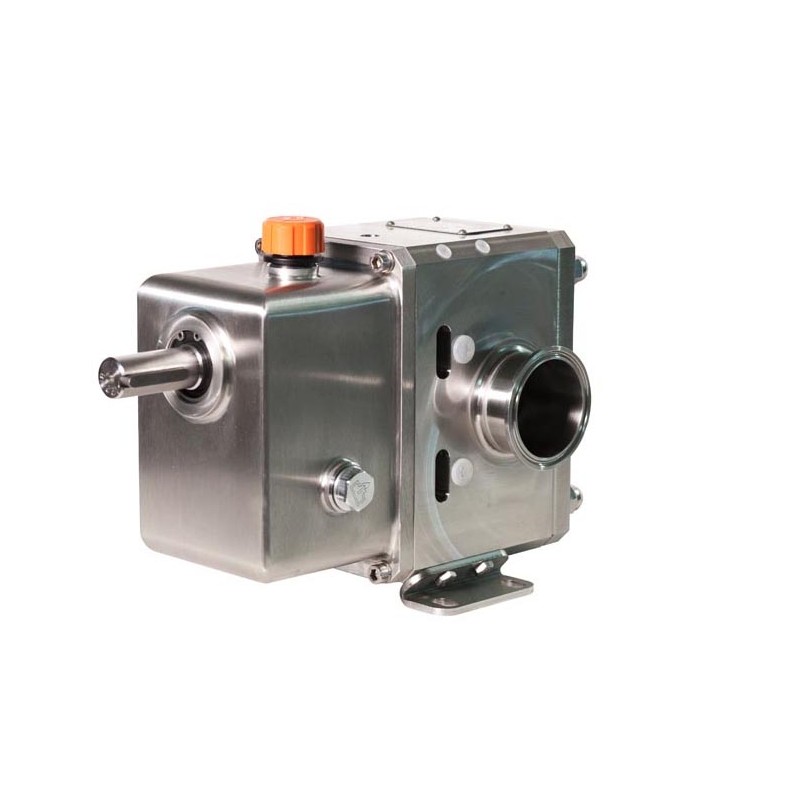
- Nuevo
Premiumlobe - Ultra-Hygienic Design
The Premiumlobe offers the ideal conditions for use in sophisticated processes.
Descripción
The Premiumlobe offers the ideal conditions for use in sophisticated processes.
- Front-loaded Seal Design
- Capacities upto 163 m3/h
- Differential pressure of 15 up to max. 80 bar
- Wetted components in 1.4404
- optional 1.4435, 1.4539, 1.4462 and Hastelloy
- CIP- and SIP-cleaning procedures are possible without any restriction
- In compliance with EHEDG
- ATEX Zone 1 / 21
The individual customer solution
The Premiumlobe offers the ideal conditions for use in sophisticated processes. Due to a conclusive concept for hygienic and non-hygienic applications it is a synthesis of highest technical know-how and practical feasibility.
The contactless running of the pump elements in rotary lobe pumps opens up important perspectives: On one hand it is perfect for hygienic applications due to the complete elimination of abrasion and product contamination; on the other hand the pump elements are wear-free with clean liquids.
An innovative design of the gearbox and the shaft configuration is part of our mission in order to improve significantly the performance of the PREMIUMLOBE compared to other pumps, mainly conventionally designed: Shafts with an extremely short shaft overhang and large diameters for maximum stiffness; preferably large bearings with high capacity in order to increase service life and reliability and to allow high pressures; selection of material with preferably low coefficient for thermal expansion in order to reduce temperature shock sensibility.
Surfaces and materials
- 1.4404 standard (equal AISI 316L) for wetted metallic material
- 1.4435, 1.4539 and 1.4462 optionally (lowest delta-ferrit contents).
- Raw material always high quality rolled steel. No use of cast iron parts due to danger of porosity
- Special "cold" welding procedures are standard.
- Electro polishing and any surface harshness up to Ra<0,4 µm are available.
Technical concept
The contactless running of the pumping elements of rotary lobe pumps opens up important vistas: On the one hand the perfect suitability for hygienic applications as abrasion and product contamination can be fully eliminated and on the other hand the non-wearing of the conveying elements when pumping clean liquids. These attributes result in minimum life cycle cost. The contactless running of the pumping elements is guaranteed while maintaining the full capacity.
This poses a challenge to the designing of the gearbox. The external bearing of rotary lobe pumps must enable the pump to hold the rotor almost concentric and on the axial level centric in the rotor case in nearly all operation situations.
However, the non-contact of the pumping elements is contradictory to the capacity. The gaps which are essential for the non-contact allow a return-flow of the pumped medium from the pressure side to the inlet site. This return-flow through the gap is called “slip” which becomes noticeable mainly when pumping low-viscous media and cares for a of the internal components of the rotary lobe pump without residues.
Mechanical aspects
Ensure the contactless running of the pumping elements
1. Bending of the shaft due to differential pressure:
The bearing and the shafts of the Premiumlobe-gearbox are designed for a minimum shaft bending which means that all models can be operated with fully contactless pumping elements at thet indicated differential pressures. And that with a high volumetric effect, i.e. with small gaps. Differential pressures up to 40 bar at cold commissioning and up to 80 bar with product can be reached. Corresponding pressure resistant housing parts, as for example connectors are chosen in accordance with the requirements.
2. Different temperature strains of the single components:
The selection of material for the components and their dimensions guarantee that the PREMIUMLOBE can run without restrictions during the CIP- and SIP-procedure, without risk of blooming at the pump case cover or pump case.
3. Settlements as well as elastic deformation of the synchronisation gearbox:
Through a new combination of force and form locking the synchronizer gear wheels are safe against settlements and loss of timing. This ensures the perfect functioning of the pump on a long term. The gearbox housings are torsion proof.
Hygiene is its strength
Free of residues through self cleaning effect (CIP / SIP)
For important operating situations the characteristic slip of the centrifugal and rotary lobe pump is a most welcome side effect as the slip significantly ensures a cleaning function if all pump elements to be cleaned – from the rotor screw to the mechanical seal – are arranged in this flow path. Only the rotary lobe pump offers this effect. FFront loaded mechanical seals (integrated to the rotor) and plane housing covers, both are standard equipment at the Premiumlobe, are imperative conditions for a cleaning without residues (CIP/SIP). Due to its innovative gearbox design the Premiumlobe can run during the CIP/SIP-procedure, even with high temperature changes. The active running of the pump during the cleaning process is imperative for an effective CIP procedure as otherwise the slip volume flow which is important for the cleaning effect, wouldn’t arise. A differential pressure of 1…3 bar is enough to achieve the self-cleaning effect of the Premiumlobe. The flow speed at the critical elements like mechanical seals, rotor screws and o-ring seals often reach upto 20 m/s. However the standard CIP flow speed in the tubes usually reaches 1.8 m/s, max. 3 m/s.
Shaft seals
Nonstop-availability due to "Front-Pull-Out"-system.
The modular structure of the PREMIUMLOBE range is of particular use regarding the sealing. All different standard gaskets are accessible from the front as "Front-Pull-Out" –system and can be exchanged by each other at any time.
The selection of the sealing principle depends on many criteria relating to the plant and the product. Standard materials for mechanical seals are SiC/SiC. The auxiliary gaskets can be made of NBR-FDA, Viton-FDA, or EPDM-FDA.
A choice of O –ring seals and lip rings complete the range of single and double acting mechanical seals.
Applications
The right pump for any application
ipp-rotary lobe pumps can be used for any individual requirements and operation conditions: For transfer, discharge (also from high vacuum), circulation and mixing, dispensing, atomizing, tank discharge and filling. Products like for example sugar, sugar coatings, starch, mashed potatoes, lard, vitamines, glucose syrup, coffee essence, lecithin, clycerine, baby food, salads, salad dressings, spices, sauces, mixings, gelatine, chocolate, dairy products etc. are part of this field of application.
78 otros productos en la misma categoría:
- Nuevo
- Nuevo
- Nuevo
- Nuevo
- Nuevo
- Nuevo
- Nuevo
- Nuevo